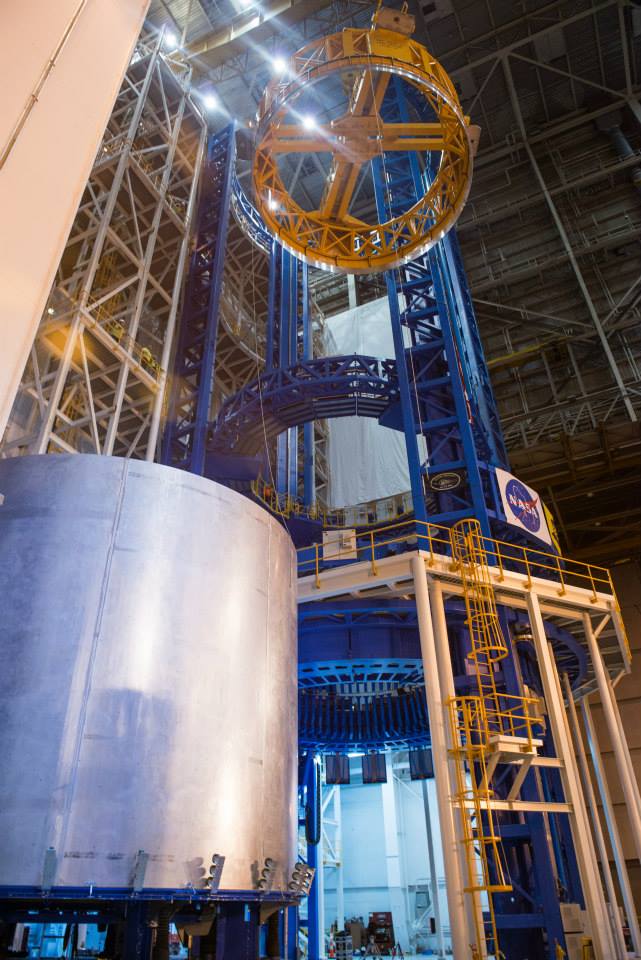
MICHOUD ASSEMBLY FACILITY, NEW ORLEANS, LA — The first pieces of rocket hardware have been loaded onto NASA’s gigantic new weld tool tasked with assembling the core stage fuel tanks for NASA’s mammoth new heavy lift rocket—the Space Launch System (SLS)—that will one day boost “Humans to Mars.”
The road to SLS production and first launch has started, with acceptance testing using parts from the over 34,000 square feet of real metal components already manufactured.
Engineers began performing the very first “confidence welds” in October on an SLS ring and barrel to ensure that the enormous 170-foot-high welder located in the newly dedicated Vertical Assembly Center (VAC) at NASA’s Michoud Assembly Facility in New Orleans works as it was designed to, before welding actual SLS flight hardware waiting in the wings.
The high-tech welding wonder was “opened for business” following a grand opening ceremony headlined by NASA Administrator Charles Bolden on Sept. 12, 2014, at Michoud, where the SLS core stage is being manufactured.
“This is the rocket that will take humans to Mars,” said NASA Administrator Charles Bolden during the Sept. 12 ribbon cutting ceremony for the SLS Vertical Assembly Center tool.
AmericaSpace was on hand for the milestone event, toured the Michoud facility, and visited the various SLS hardware components up close.
“The critical path for this rocket goes through this machine here,” said SLS Program manager Todd May at the dedication. “We passed our critical design review on the core.
“There is over 34,000 square feet of hardware sitting in this factory ready to come here and be welded up.
“The team is really anxious to get though the acceptance testing and start putting hardware though it.”
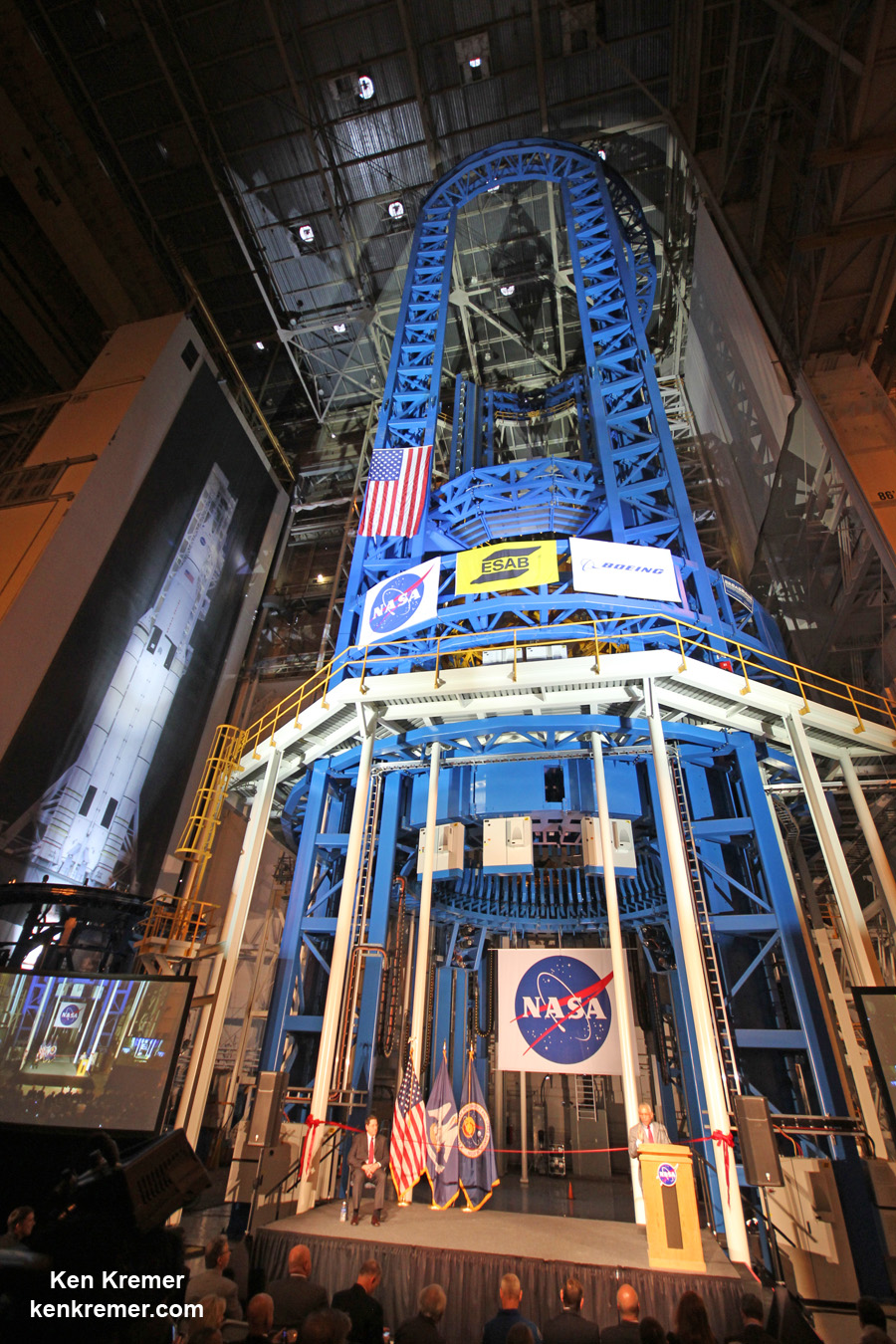
NASA’s colossal Space Launch System (SLS) rocket will be the world’s most powerful rocket ever built in history. The SLS is being developed to propel astronaut crews in the Orion spacecraft to deep space destinations including asteroids and the Red Planet.
The VAC is the world’s largest spacecraft welding tool and technicians will use it to integrate the components of the cryogenic liquid hydrogen and liquid oxygen fuel tanks for the SLS core stage.
“When you see something like this [welder] and you look up and see the size of this thing you can’t help but understand and realize that this thing is real,” said May.
“Before it was just a concept. And now you’re looking at a tool.
“Every bolt and piece that came together to make this [welding] tool has happened in less than 3 years. We have a nationwide team with great partners including Boeing, ATK, Aerojet Rocketdyne and sister NASA teams. SLS has over 500 contractors in 42 states working to pull this together.
“It’s amazing to be here and look at this tool.”
The core stage is comprised of five major structures: the forward skirt, the liquid oxygen tank, the intertank, the liquid hydrogen tank, and the engine section.
The tanks for the very first SLS core stage will be assembled soon by joining domes, rings, and barrels together in the Vertical Assembly Center by a process known as friction-stir welding.
The rings connect and provide stiffness between domes and barrels. All of the flight rings for the first SLS core stage have already been welded.
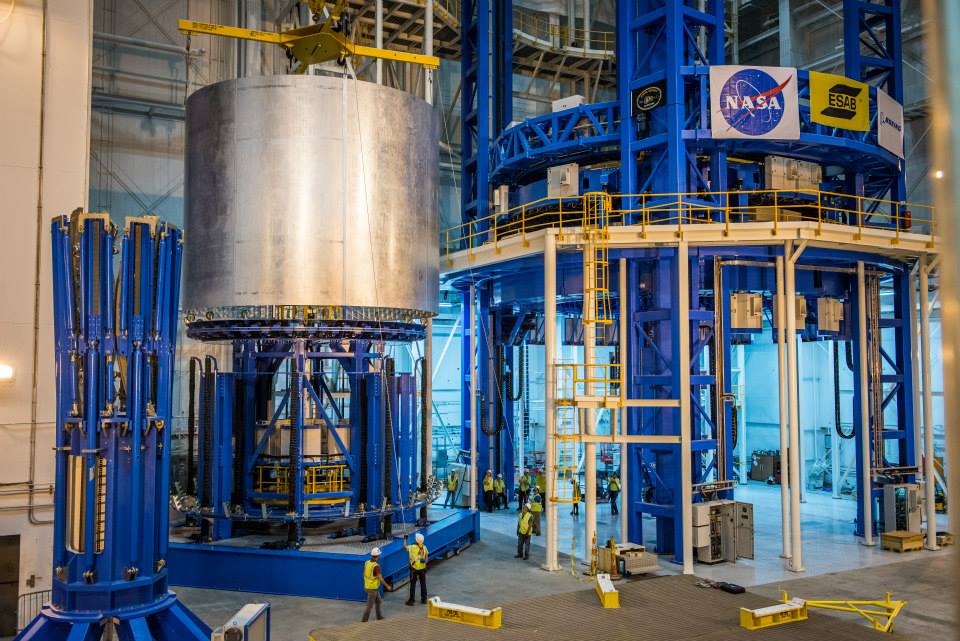
To date, 10 barrels have been produced, including the first four liquid hydrogen qualification barrels, for the SLS core stage. Whole barrels for the two pressurized tanks, the forward skirt, and the aft engine section are welded together from barrel panels using Michoud’s specially designed Vertical Weld Center (VWC) tool.
So the barrel panels are welded together in the VWC and then the completed barrels are fed into the VAC.
NASA says that nearly 1/2 mile of friction-stir welds in Michoud’s family of new SLS welders have already been successfully completed to produce the rings, barrels, and domes.
The core stage stores the cryogenic liquid hydrogen and liquid oxygen propellants. They will feed the vehicle’s quartet of RS-25 space shuttle main engines at the base, which have been repurposed to provide the propulsion and power the core stage.
Altogether, 16 of the RS-25 engines are being adapted and tested at the Stennis Space Center in Mississippi.
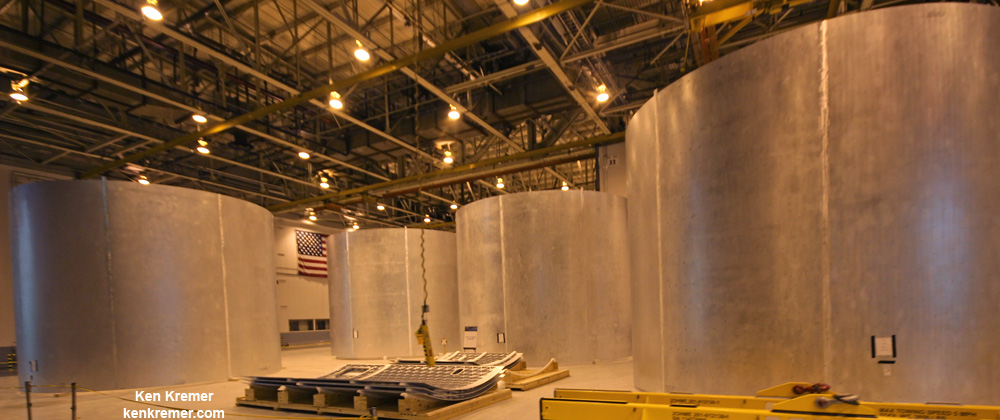
The SLS core stage towers over 212 feet (64.6 meters) tall and sports a diameter of 27.6 feet (8.4 m).
Overall, the SLS measures 322 feet and generates 8.4 million pounds of thrust.
Boeing is the prime contractor for the SLS core stage and its avionics.
To get an idea of just how big the welder and SLS core stage really are, May gave an illuminating description.
“This [VAC] tool itself is only the length of 1 hydrogen tank of the core stage,” May elaborated.
“The whole core would stick up another 50 feet through the roof of this building. Then on top of that you have Orion and its 100 foot stack.
“So here you see how massive the SLS rocket really is. And it takes a massive tool to build this massive rocket that will take humans out beyond low Earth orbit and beyond the bounds that have held us for the past 40 years!”

The VAC checkout and weld testing process ensure that the welder operates as planned and will take a few weeks, starting in October, said NASA Associate Administrator Robert Lightfoot during an interview with AmericaSpace at the recent dedication ceremony at Michoud.
Multiple domes, rings, and barrel segments have already been manufactured and await delivery into the VAC welder for integration to produce the maiden core stage unit.
The SLS core stage builds on heritage from NASA’s Space Shuttle Program and is based on the shuttle’s External Fuel tank. All 135 flight units were built at Michoud during the 30-year-long shuttle program.
The inaugural test flight of the SLS on the EM-1 mission is targeted for November 2018. It will be configured in its initial 70-metric-ton (77-ton) lift capacity version.
The SLS EM-1 flight will launch an uncrewed Orion spacecraft on a roughly three-week-long test mission journeying beyond the Moon to a distant retrograde orbit, according to William Gerstenmaier, associate administrator for the Human Explorations and Operations Mission Directorate at NASA Headquarters in Washington.
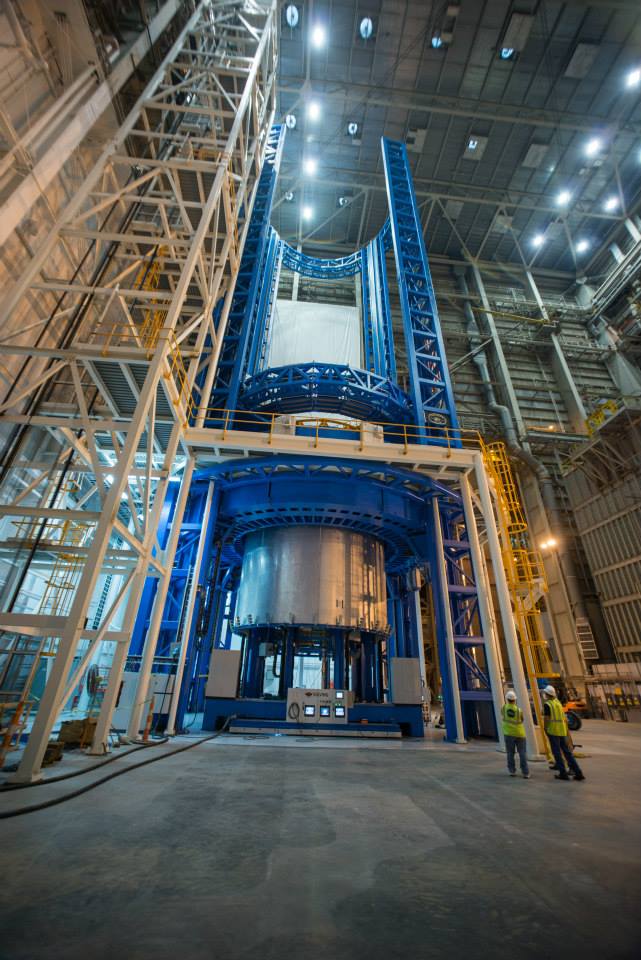
Over time the SLS will evolve into an unprecedented 130 metric tons (143 tons) lift capacity version to enable NASA’s human missions to the Red Planet and other places in the Solar System.
“The road to Mars and asteroids begins right here at Michoud … and Mississippi,” said NASA Administrator Charles Bolden. “This NASA rocket is a game changer for deep space exploration.
“The SLS will launch NASA astronauts to investigate asteroids and the surface of Mars while opening new possibilities for science missions as well.”
Be sure to read about the VAC Welder dedication ceremony at Michoud here.
Stay tuned here for continuing updates.
Want to keep up-to-date with all things space? Be sure to “Like” AmericaSpace on Facebook and follow us on Twitter: @AmericaSpace
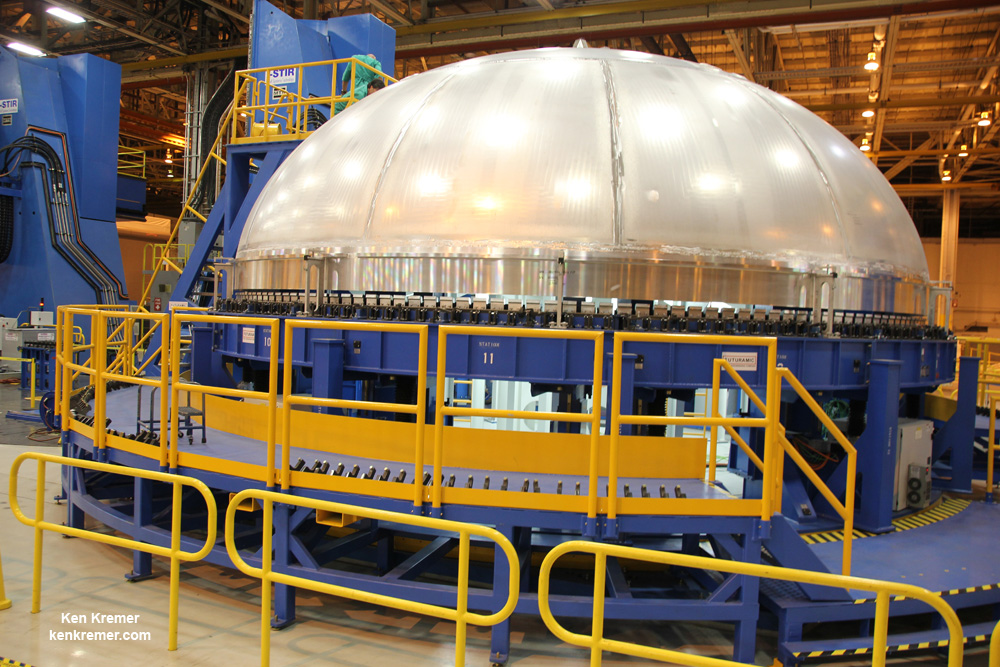
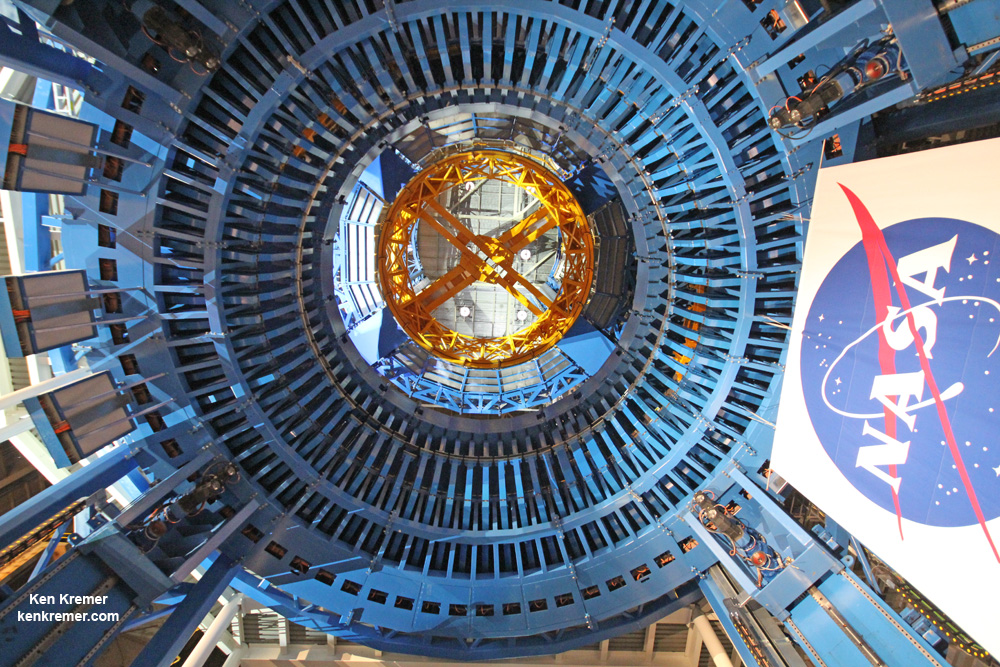
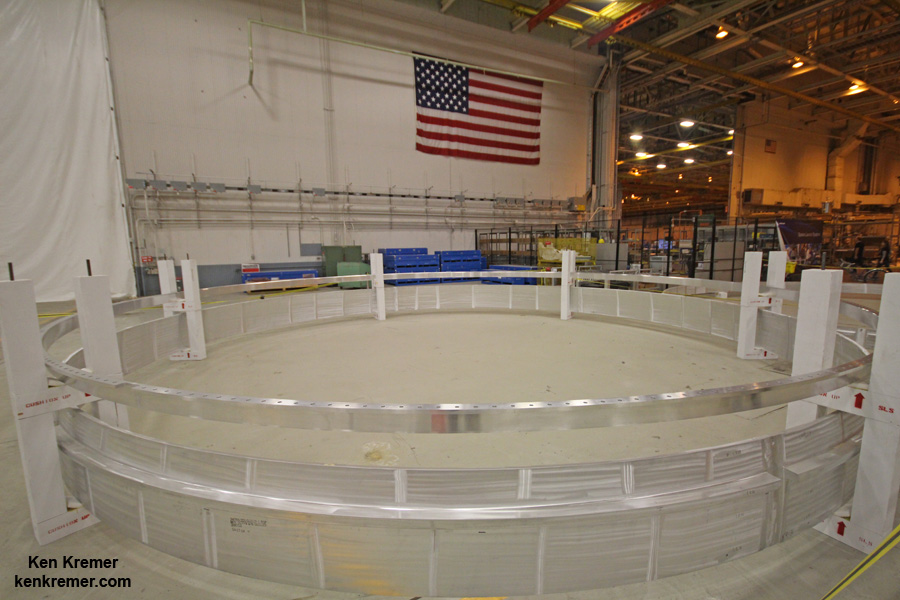
And thus, all those who painted SLS as a powerpoint only rocket are made lie-tellers and frauds.